FMEA通過對產(chǎn)品或過程中的潛在故障模式進(jìn)行預(yù)測和評估,幫助組織識別并優(yōu)先處理那些可能導(dǎo)致嚴(yán)重后果的故障模式,從而實現(xiàn)風(fēng)險的有效管理。這種方法的核心在于預(yù)防和減少故障的發(fā)生,從而提高生產(chǎn)效率、保證產(chǎn)品質(zhì)量并降低運(yùn)營成本。
一、FMEA的基本原理
FMEA基于一種假設(shè),即任何產(chǎn)品或過程都可能存在潛在的故障模式。通過對這些故障模式進(jìn)行詳細(xì)地分析和評估,可以確定它們對產(chǎn)品或過程性能的影響程度,并據(jù)此制定相應(yīng)的預(yù)防措施。FMEA通常包括以下幾個步驟:1.確定分析范圍:明確要進(jìn)行分析的產(chǎn)品或過程,并確定分析的重點(diǎn)和目標(biāo)。
2.故障模式識別:通過收集和分析歷史數(shù)據(jù)、專家意見等信息,識別產(chǎn)品或過程中可能出現(xiàn)的故障模式。
3.影響評估:對每個故障模式的影響程度進(jìn)行評估,通常從嚴(yán)重度(Severity)、發(fā)生度(Occurrence)和檢測度(Detection)三個方面進(jìn)行。
4.優(yōu)先級排序:根據(jù)評估結(jié)果,對故障模式進(jìn)行優(yōu)先級排序,確定需要優(yōu)先處理的故障模式。
5.制定預(yù)防措施:針對優(yōu)先級較高的故障模式,制定相應(yīng)的預(yù)防措施,并監(jiān)控實施效果。
在TPM咨詢中,F(xiàn)MEA被廣泛應(yīng)用于生產(chǎn)過程的改進(jìn)和優(yōu)化。通過FMEA分析,可以識別出生產(chǎn)過程中潛在的故障模式,進(jìn)而制定相應(yīng)的改進(jìn)措施,提高生產(chǎn)過程的穩(wěn)定性和可靠性。同時,F(xiàn)MEA還有助于培養(yǎng)員工的預(yù)防意識和風(fēng)險管理能力,形成持續(xù)改進(jìn)的文化氛圍。
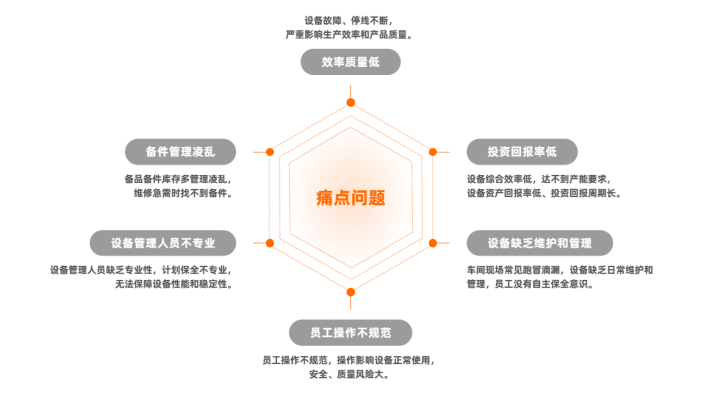
綜上所述,故障模式與影響分析(FMEA)是TPM咨詢中一種非常重要的工具。通過FMEA分析,組織可以更加有效地識別和管理風(fēng)險,提高生產(chǎn)過程的穩(wěn)定性和可靠性,從而實現(xiàn)持續(xù)改進(jìn)和創(chuàng)新。同時,也需要注意到FMEA的局限性,并在實際應(yīng)用中采取相應(yīng)的措施加以克服。
文章說明:本文來自網(wǎng)絡(luò),感謝作者,如有版權(quán)問題,請聯(lián)系客服處理。感謝您對優(yōu)制咨詢的關(guān)注和支持!